One of Singapore’s leading ready-mixed concrete suppliers, Island Concrete – a subsidiary of Hong Leong Asia (HLA) – celebrates its 55th anniversary this year. SEAC talked to Simon Loh, chief operating officer of HLA’s Building Materials Group Singapore, about the company’s progress and innovations, and how it embraces the future.
1). Mr Loh, congratulations as Island Concrete marks another milestone. What is the company’s strategy to maintain its competitive edge?
Simon Loh (SL): Over the past five decades, Island Concrete has been an industry-leading brand in the built environment sector known for its product quality, timely delivery, and the scale to supply even the largest of projects – such as Marina Bay Sands.
We continuously innovate through working closely with our customers – from developing a new or improved product to offering urban solutions, which adds value to the business. This includes the commitment to shift towards a lower-carbon and more circular economy, helping to deliver sustainable and responsible cities of the future.
Looking ahead, we will continue to leverage our expertise and industry partnerships to ensure supply chain resilience to meet the needs of our customers. Reliable, resilient and responsible – the 3Rs – will be one of the mainstays of Island Concrete’s continued relevance and growth.
2). Island Concrete has recently implemented several initiatives to improve productivity. Among them is to upgrade the company’s fleet of concrete mixer trucks from regular 9 cu m to 12 cu m. Can you share more on the benefits of having these larger-capacity trucks?
SL: We have been upgrading our concrete mixer trucks from 9 cu m to 12 cu m since 2022. Many of our sub-contractors have also done so. At the end of 2024, these 12 cu m concrete mixer trucks already made up more than 40% of Island Concrete’s trucking fleet in Singapore. Based on this figure, we would have eliminated more than 138,000 trips in a year.
This not only reduces road congestion and carbon footprint, but also reduces demand for truck drivers while at the same time increases their remuneration for each trip. On top of that, site casting can be completed much faster with shorter waiting times. Overall, the waiting time for each 12 cu m truck to offload on site has been reduced by about 20% compared to that using a 9 cu m truck.
3). As you mentioned earlier, Island Concrete also adopts greener practices. One of the company’s efforts is to manufacture green concrete with alternative materials such as fly ash and ground granulated blast furnace slag (GGBS). How much CO2 emissions can be saved by using this green concrete?
SL: Enviromix, one of the eco mixes offered under Island Concrete, allows approximately 20% emission reduction compared to regular concrete. The performance of green concrete is also similar to traditional concrete.
Our green concrete was used in the construction of CapitaSky – a 31-storey Grade A office building on 79 Robinson Road. Recent projects that will also use our green concrete include the new NS Square at Marina Bay (which will replace The Float @ Marina Bay) and an executive condominium in Tengah Plantation.
In addition, our latest batching plant in Pulau Punggol Timor, in northeastern Singapore, is expected to be commissioned by the second quarter of 2025. This plant is designed with sustainability in mind. It will feature larger, more efficient mixers as well as a conveyor system that helps minimise carbon footprint and labour inputs.
4). In today’s fast-paced work environment, what kind of training does Island Concrete provide to ensure that its staff and technicians are equipped with the necessary skills and knowledge?
SL: Technical training sessions, both on the job and in classrooms, are essential to upgrade and enhance the skills of our employees and production technicians. Apart from the internally conducted training courses, our employees are also encouraged to attend external training programmes on hard skills, such as how to leverage concrete technology or enhance productivity and efficiency in modern construction with advanced materials, courses administered by recognised institutes like ACI (American Concrete Institute) – Singapore Chapter.
5). The construction landscape in Singapore has changed so much over the last few years, especially since the pandemic. What do you see as the biggest barrier(s) in this market?
SL: One of the challenges the industry faces is the slow adoption of new technologies and practices. In general, the industry possesses a somewhat conservative outlook towards new technologies and practices. The focus has always been about accumulating successful track records; gaining confidence before new technologies and practices can take off, which is understandable as mistakes can be costly. Another part of this may also be due to the imbalance in the allocation of risks vs rewards amongst the various stakeholders, especially during the early introductory stages of the new product and technology lifecycle.
Most tend to take the ‘follow the leader’ approach, letting others prove the success before adopting for their own use. This leads to slower adoption and changes. Regulatory push or tweaking the risk vs rewards balance might also be a good way to encourage quicker adoption.
6). In addition to digitalisation and sustainability, do you see other trends emerging in the ready-mix concrete sector?
SL: High-performance concrete seems to hold good promise in Singapore’s construction industry. As our structures get taller and selling price of space increases, high-strength concrete gives the advantage of handling the higher stresses with a smaller column cross-sectional area. Concrete with good chloride resistance could also be an important part of the product portfolio, especially when we deal with structures that are needed to tackle rising sea levels.
7). Speaking of innovation, Island Concrete is currently collaborating with industry partners to develop an autonomous wheel loader at Jurong Port’s Ready-Mixed Concrete (RMC) Ecosystem. Can you tell us more about this latest initiative?
SL: The autonomous wheel loader is still in the development stage. Once ready, we will pilot at the Jurong Port RMC initially. Once the concept has been proven, we intend to deploy at least eight units across the island. They will function as an integral part of our batching plant, with each machine having a load capacity of up to 6 t.
Fitted with sensors and cameras, the wheel loader will be operated unmanned and controlled through a system software. Whenever raw materials inventory in the storage hopper is low, sensors laid in the raw materials storage section of the batching plant will kick in and the storage hopper will activate the loading process until the hopper is fully loaded.
The wheel loader will select and load the correct raw material into the correct storage hopper. After the raw material is fully replenished, the machine will return to its charging station and await further instructions. Unless there is a malfunction, there will be no need for human intervention.
This autonomous wheel loader can operate round-the-clock and is suitable for long, continuous operations. As the machine is electrically powered, its carbon footprint will be lower than that of the traditional diesel-powered model.
Such an initiative will enhance our operational efficiency and reduce demand for wheel loader drivers, while improving safety. It will also enable the redeployment of headcount to carry out more complex tasks.
If the pilot run at the Jurong Port RMC Ecosystem is successful, we intend to replicate the process across our other batching plants when feasible.
Note: This story has also been published in the May/Jun 2025 issue of SEAC. Click here to read online or here to download the PDF file (pages 46-48).
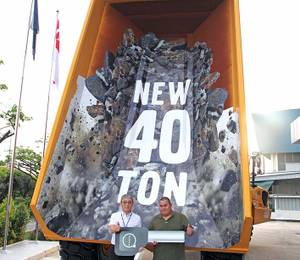
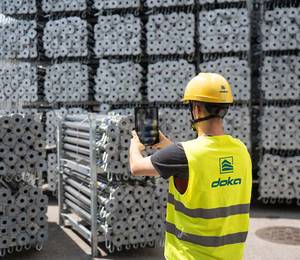
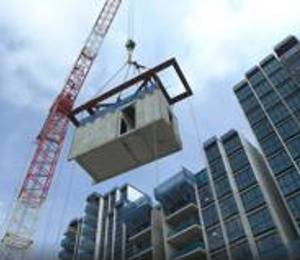
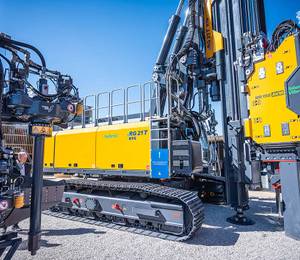
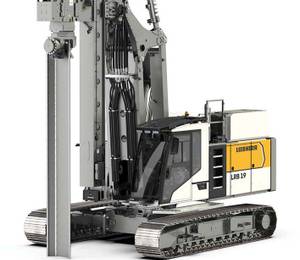
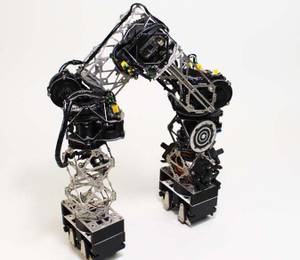
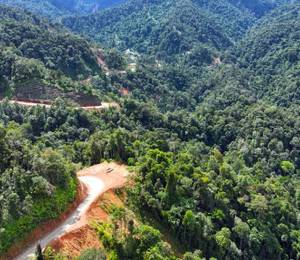